Intervista Giulio Dal Lin
"The basic idea was to adopt the lean approach in its entirety […] and lay the foundations for a culture of excellence."
When did CAREL first start talking about lean?
Our first contact with lean thinking principles and techniques dates back to 1994, when CAREL's President, Luigi Rossi Luciani, took part in the first seminars in Veneto on lean philosophy and its applicability to the Veneto industrial system. The workshops featured weekly sessions spanning 6 months, and saw the participation of leading academics on the subject, such as Prof. De Toni, Prof. Filippini, Prof. Forza and Prof. Vinelli, as well as a small number of interested businesspeople. The result was the desire to transform CAREL into a lean company.
At the same time as the seminars, Rossi decided to hold weekly meetings with a group of managers, with an original format: each manager had to take turns commenting on a chapter from the book "The machine that changed the world". An effective method for introducing lean concepts at CAREL.
How long did it take for lean to become structured at CAREL?
The actual transformation began a few years later, starting in late 2006; the basic idea was to adopt the lean approach in its entirety, i.e. not limited merely to applying tools and techniques, but rather transforming the company and bringing about a change in culture, behaviour, how we work together. In other words, something that would last over time and was able to lay the foundations for a culture of excellence. This required engagement at all levels, by understanding why we wanted to move in this direction, fostering change in small yet constant steps. Values such as team spirit, the desire to improve existing processes by reducing waste, visibility and transparency of actions, the need to break down communication barriers, and the desire to put value for the customer in the centre of our discussions. Yet also avoiding the trap of "resting" on our positive results, rather striving to be in constant "mutation", so as to guarantee the growth and development of the organisation in the face of an increasingly competitive market.
What were the main obstacles?
The first obstacle, if it can be called that, was that CAREL at the time was already a successful company, without an evident need to undertake any transformation. Solid revenues, strong growth, generally satisfied customers. However, there were some early signals pointing to the need to "do something". Firstly, our growth had led to the company becoming increasingly complex and structured, with the risk of creating potential organisational silos that were less connected and less open than in the past. This increasing complexity also meant generally longer process lead times in both production and product development. There was also a general difficulty in coordinating more complex initiatives and a lack of transparency and visibility of what was being done by the different work teams. Finally, there was the need to better disseminate our corporate strategy and then put it into practice. All these signals, if read against the backdrop of our results, could have been considered as just "part of the game", however to the attentive eyes of the company's owners required a response, so as to avoid standing still. Hence the desire to start adopting a lean perspective.
"There was the need to better disseminate our corporate strategy and then put it into practice."
Which departments/offices were involved in the beginning?
The transformation commenced in R&D and Operations. In R&D, there was the need to help colleagues improve the product development process, mutual collaboration and work organisation. Indeed, projects were becoming more complex to manage, both in terms of the tasks required and the people involved. Many people were in fact working on multiple projects at the same time, with a consequent loss of focus and energy. The result was longer project times, and even some quality problems. Our response was to create compact teams, introduce visible planning, with a "one project flow", similar to the concept of one piece production flow. Thanks to this approach, project delays were slashed.
In Operations, on the other hand, the key driver of change was the creation of "value streams": we shifted from a logic based on production departments and batch and queue mechanisms, to the creation of value streams, with the organisation that supports the value stream residing in the gemba, i.e. near the production lines. The one piece flow concept was fundamental in supporting CAREL's business model: production in important niches, at times in small quantities, to meet customer needs. For example, work islands were created, with a significant improvement in ergonomics.
The following lean "basics" were introduced in all areas: PDCA, visible planning, 5S; essential to ensure participation, engagement and contribution from the entire organisation. Lean, in Operations, has made it possible to improve indicators on safety, quality, compliance with delivery times, and costs.
When did this philosophy start to be shared with the branches, and which branches were involved first? How did the branches welcome this change?
The branches started to get involved in around 2013, with the aim of extending the benefits brought about by the introduction of lean thinking across all the Group’s organisations. Our branches are very important in this sense, as they have a direct contact with customers and are very close to market needs.
The first branches to get involved were in Europe, starting with CAREL Deutschland, and then later those outside of Europe, in particular in Asia and the Americas. The actions taken at our branches were based on several principles: simplify internal processes by bringing visibility to order flow and critical performance KPIs for customers, involving the different departments at the branch; introduce lean concepts such as PDCA, in order to ensure everyone’s extensive contribution in terms of continuous improvement and innovation; better structure improvement projects in all interaction processes between branches, and between branches and HQ, where we know there is great potential for simplification and improvement, given our strong growth.
Today, how many people are involved in lean across the Group?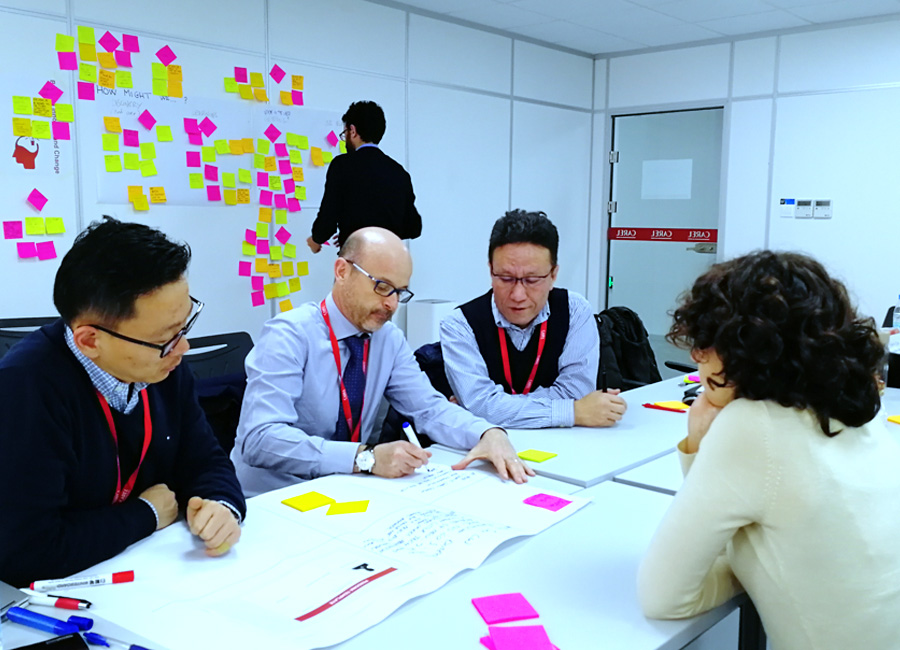
Around 2000… it’s our mission!
In other words, every person who works at CAREL needs to be able to apply the principles and values of continuous improvement in their day-to-day work.
With this in mind, we established the role of Lean Ambassador a couple of years ago, a part-time position available to anyone who wants to actively participate in the development of the company’s lean program.
In terms of lean organisation, on the other hand, there are around 15 people across the Group who work full time in the lean area, who are responsible for projects and liaise with the different departments.
Today, the Lean Department represents our competence centre for:
-
Continuous improvement (Lean + six sigma)
-
Innovation processes (including business model generation, design thinking…)
-
Project management
-
Lean training
-
Hoshin Kanri
What does the future hold for lean at CAREL?
Lean at CAREL has expanded in scope and competences and is being "updated" in the light of new company needs, market challenges and external innovation trends. It always refers to “traditional” lean, understood as the principles, tools and methods that derive from the Toyota Production System and from the lean model described by Womack, Jones, and others.
This aspect should not be underestimated: the basic principles of lean are "simple", yet at the same time "powerful", to ensure growth and stability. It is therefore essential to constantly review and "maintain" our processes.
Recently we have introduced the aspects of process innovation and business innovation (the name of the office was also changed accordingly). This involved embracing the design thinking and business model generation approaches. A further boost was given by our first steps in adopting Agile and Scrum, with certification of our first Scrum Masters and Product Owners.
The Lean Department today has increased its competences in project management, taking the helm in several strategic company projects. The other challenge involves post M&A integration, specifically working on a standard on acquisitions, and how to combine the revolution brought by Industry 4.0 (now 5.0) and lean principles.
There is certainly no lack of variety!